Understanding Tubing Connector Types: A Comprehensive Overview
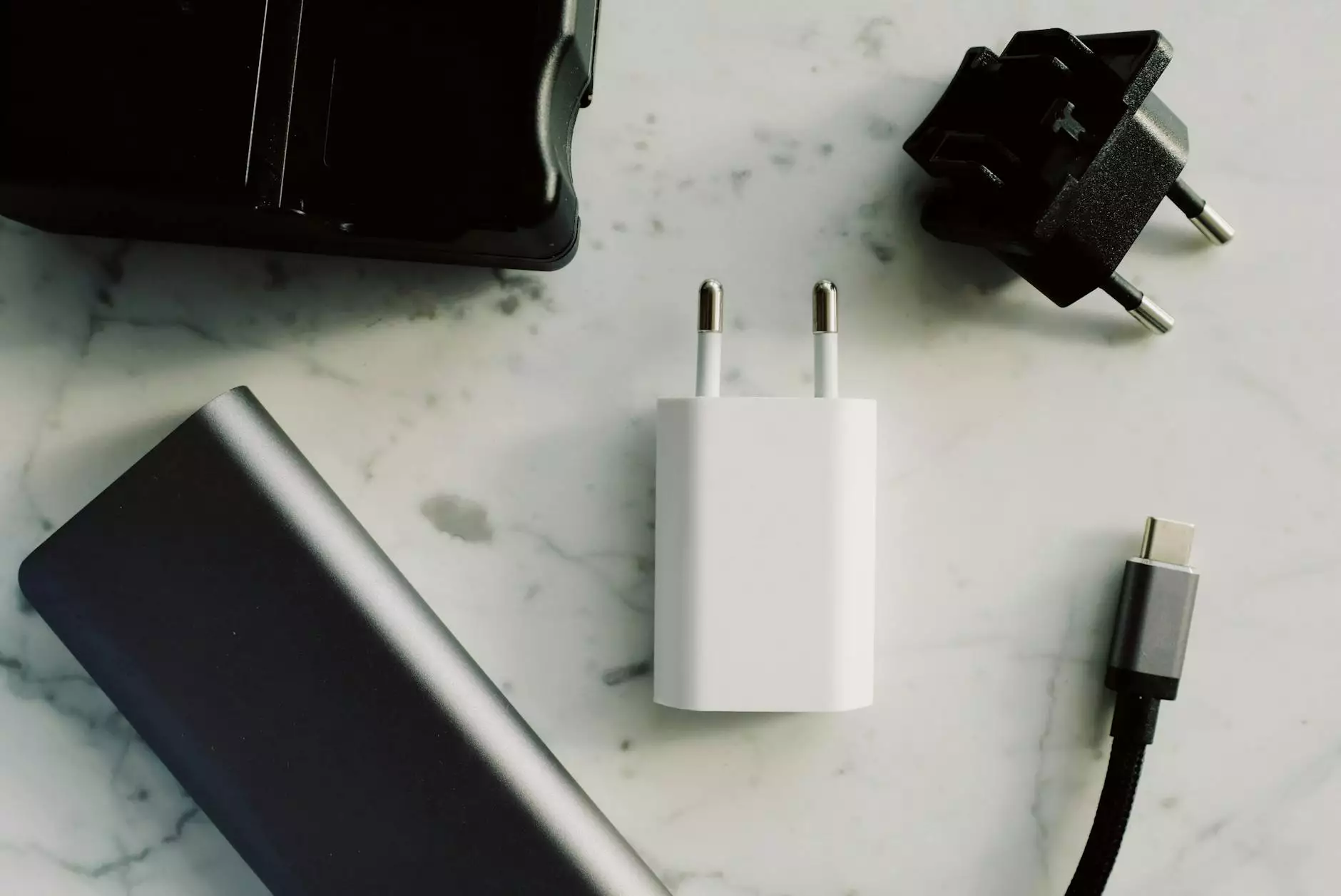
In today’s industrial landscape, tubing connectors form the backbone of many applications across various sectors. These connectors ensure that fluid, gas, and other materials can move seamlessly through systems, and they are crucial for the efficiency and safety of designed processes. At techtubes.in, we specialize in a wide range of tubing fittings and connectors designed to meet the diverse needs of our customers.
Types of Tubing Connectors and Their Applications
There are several types of tubing connectors, each serving unique functions. Understanding these tubing connector types is pivotal for engineers, procurement managers, and technicians alike. Below, we delve into the most common types used in industry today.
1. Tube Fittings
Tube fittings are essential for connecting two tubes in fluid systems. They provide a reliable seal to prevent leaks and are vital for various applications, including hydraulic and pneumatic systems. The types of tube fittings include:
- Compression Fittings: These create a tight seal by compressing a ring (ferrule) against the tubing.
- Weld Fittings: These are welded directly to the tubing, offering stronger and permanent joint connections.
- Flare Fittings: These involve flaring the end of the tubing to create a male connection that tightens against a female threaded fitting.
Each fitting type has its own advantages and is selected based on specific application needs.
2. Ferrule Fittings
Ferrule fittings utilize a ferrule to create a seal between the tubing and the fitting itself. This type offers:
- Durability against vibration and extreme temperatures.
- Easy connections and disconnections due to their design.
- Resistance to corrosion, making them suitable for various environments.
Ferrule connectors are widely used in hydraulic applications and can handle high-pressure situations effectively.
3. Forged Pipe Fittings
Forged pipe fittings are manufactured through a forging process, which gives them greater strength and integrity than cast fittings. Important characteristics include:
- High tensile strength to withstand extreme pressures.
- Better durability over time compared to other fitting types.
- Variety in design, including elbows, tees, and adapters.
They are commonly used in high-pressure applications such as oil and gas piping systems.
4. Threaded Pipe Fittings
Threaded pipe fittings feature threads on both the inside or outside and are used to connect pipes in a tight and leak-proof manner. Key benefits include:
- Ease of installation and removal.
- Compatibility with a variety of pipe materials.
- Versatility, as they can be used in multiple applications from water to gas systems.
They are often employed in residential and commercial plumbing.
5. Flanges
Flanges are flat pieces of material used to connect two sections of piping systems. They provide a stable connection that can be easily bolted together. Advantages of flanged connections include:
- Robust joints that can handle high pressures.
- Ease of maintenance, as flanges can be unbolted for cleaning or replacement.
- Support for several pipe diameters and materials.
Flanges are vital in chemical and petrochemical industries due to their ability to manage pressure and temperatures.
6. Valves
Valves are crucial components that control the flow of fluids within pipelines. Various types include:
- Check Valves: Prevent backflow in a piping system.
- Ball Valves: Provide tight sealing with minimal fluid resistance.
- Needle Valves: Offer precise flow control, ideal for low flow rates.
- Manifold Valves: Allow control of multiple inlets and outlets, widely used in HVAC systems.
Each valve type plays a significant role in ensuring that systems operate smoothly and efficiently.
Choosing the Right Tubing Connector Types
Selecting the appropriate tubing connector type involves considering factors such as:
1. Pressure Requirements
The operating pressure of the system will dictate the kind of connector required. High-pressure applications necessitate connectors with robust construction like forged pipe fittings.
2. Temperature Conditions
Temperature variations can affect the materials used in tubing connectors. It's crucial to choose materials that can withstand the operational temperatures without degrading.
3. Material Compatibility
Ensure compatibility between tubing connectors and the fluids being transported. For instance, corrosive chemicals require specially coated or stainless steel connectors.
4. Ease of Installation and Maintenance
Consider the installation process and whether the connectors will need frequent maintenance. Some designs allow for quicker assembly and disassembly.
5. Cost Efficiency
While it may be tempting to go for lower-cost options, consider the long-term value and durability of the connectors chosen. Investing in quality connectors may reduce future replacements and maintenance costs.
Conclusion
Understanding the various tubing connector types is essential for anyone involved in the planning, implementation, or maintenance of fluid or gas transport systems. The right choice of fittings and connectors not only enhances the performance of your systems but also contributes to safety and efficiency.
At techtubes.in, we offer a comprehensive range of high-quality tubing connectors, including tube fittings, ferrule fittings, forged pipe fittings, threaded pipe fittings, flanges, and an extensive assortment of valves. Our expert team is ready to assist you in selecting the tools tailored to your needs, ensuring that your systems function flawlessly.
Explore Our offerings
Visit our website techtubes.in to explore our full range of products and discover how our tubing connector types can meet your specific industrial needs.