Understanding Precision Injection Molding: A Key to Manufacturing Success
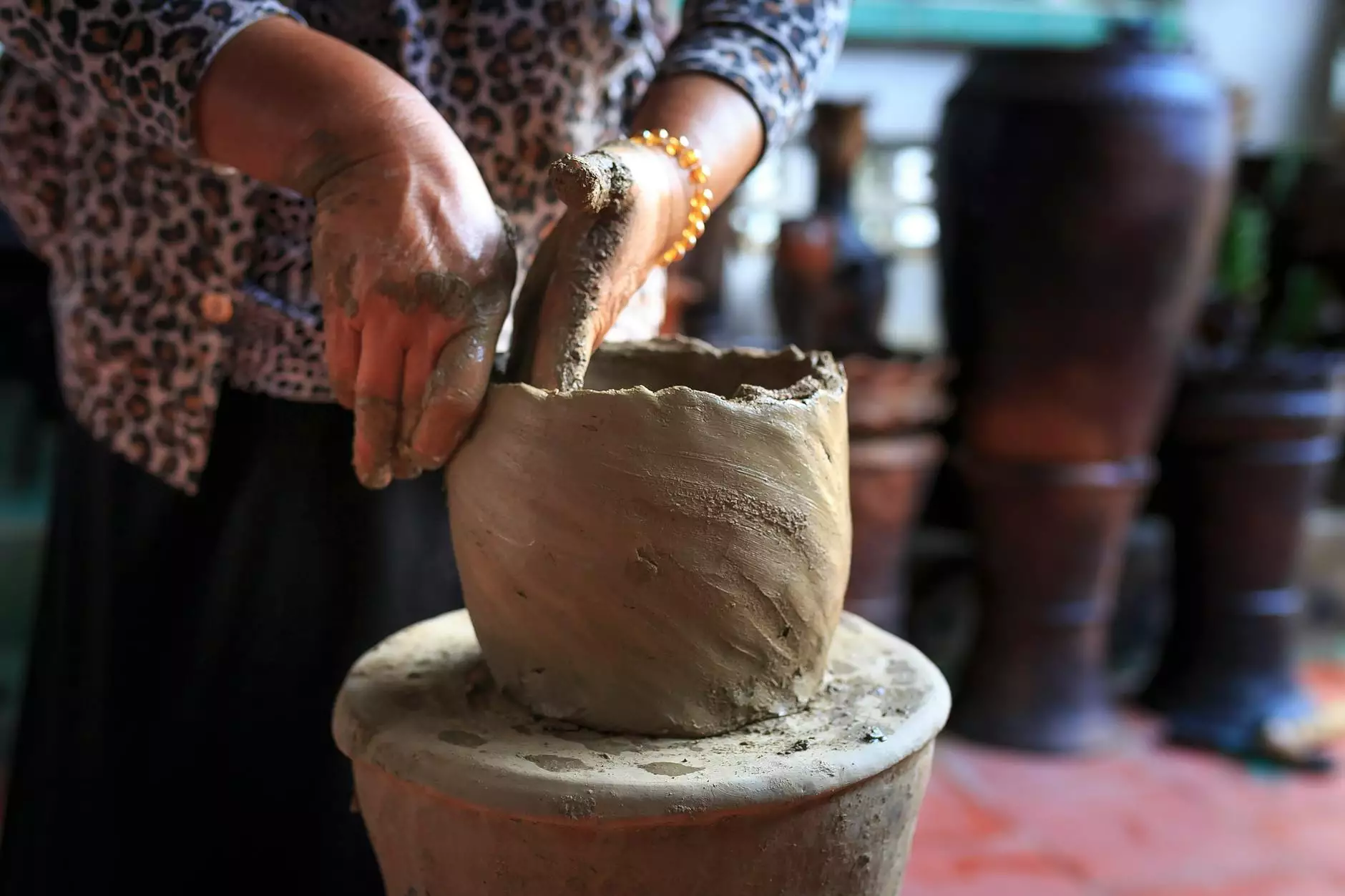
In the ever-evolving landscape of manufacturing, precision injection molding stands out as a critical technique that enhances production efficiency and product quality. For businesses, especially those in the realm of metal fabrication, mastering this process can lead to significant competitive advantages. This article dives deep into the intricacies of precision injection molding, its applications, benefits, and how it integrates seamlessly into modern manufacturing processes.
The Basics of Precision Injection Molding
Precision injection molding is a manufacturing process that involves injecting molten material into a mold to create precise and complex parts. While traditionally associated with plastics, recent advancements have expanded its applications to various materials, including metals. This method is characterized by its ability to produce parts with narrow tolerances, intricate geometries, and superior surface finishes.
How Does Precision Injection Molding Work?
The precision injection molding process can be broken down into several key stages:
- Material Preparation: Raw materials are prepared, often in the form of pellets or powdered metal, depending on the desired end product.
- Heating: The materials are heated to a temperature where they become molten and can be easily injected into the mold.
- Injection: The molten material is injected into a precisely designed mold at high pressure, filling every cavity of the mold.
- Cooling: The filled mold is cooled to solidify the material, forming the final part.
- Demolding: Once cooled, the mold opens, and the finished part is ejected.
- Finishing: Any additional finishing processes, such as trimming or surface treatment, are performed to meet specifications.
Advantages of Precision Injection Molding
Implementing precision injection molding in manufacturing processes can yield numerous advantages:
1. High Accuracy and Precision
One of the most significant benefits of precision injection molding is its ability to produce parts with outstanding accuracy. This precision ensures that each component meets exact specifications, which is crucial in industries such as aerospace, automotive, and medical equipment manufacturing.
2. Cost-Effective Production
While the initial setup for precision injection molding may be higher than other methods, the efficiency of the process often results in a lower cost per unit when large quantities are produced. This method is exceptionally beneficial for mass production scenarios.
3. Complex Geometries
The capability to create complex shapes that would be challenging to achieve with other manufacturing processes is another advantage of precision injection molding. This flexibility allows for innovative designs and solutions.
4. Minimal Waste
Precision injection molding optimizes material use thanks to its closed-loop system, which significantly reduces waste. Over time, this not only benefits the environment but also lowers material costs for manufacturers.
5. Consistency and Repeatability
Once the molds are created and the process is set up, precision injection molding allows for consistent and repeatable production quality. This reliability is vital for industries that demand stringent quality controls.
Applications of Precision Injection Molding
The applications of precision injection molding span various industries. Here’s a detailed overview of its most common applications:
Aerospace Industry
The aerospace industry often requires components that are not only lightweight but also incredibly durable. Precision injection molding provides parts that meet these rigorous demands while ensuring compliance with strict safety regulations.
Automotive Industry
In automotive manufacturing, precision injection molding is used to create intricate parts such as dashboards, door panels, and housing for lights and mirrors. The technique allows for lower weight components, which contribute to overall fuel efficiency.
Medical Devices
The production of medical devices necessitates high precision and cleanliness. Precision injection molding meets these requirements, making it integral to the manufacturing of syringes, surgical instruments, and other critical components.
Consumer Electronics
In the consumer electronics sector, the need for compact and lightweight components has led to the widespread use of precision injection molding. It is commonly used for producing casings, connectors, and internal parts of various electronic devices.
The Role of Deep Mould in Advancing Precision Injection Molding
At Deep Mould, we understand the transformative power of precision injection molding in driving business success. Our expertise lies in delivering state-of-the-art solutions tailored to meet the evolving needs of various industries. By focusing on high-quality metal fabrication processes, we help our clients achieve their production goals without compromising on quality or precision.
Expert Consultation and Support
Our team of experts is dedicated to providing comprehensive consultation services that allow clients to make informed decisions about their manufacturing processes. By understanding your specific needs, we can recommend the best approaches utilizing precision injection molding that align with your business objectives.
Advanced Technology and Equipment
Deep Mould invests in the latest technology and equipment to ensure that we deliver optimal results. Our cutting-edge machinery and software facilitate efficient design, mold creation, and production, resulting in components that consistently meet stringent tolerances and performance criteria.
Streamlined Production Processes
Our streamlined production workflows are designed for efficiency and effectiveness. By minimizing downtime and maximizing output, we can meet the demands of high-volume production without sacrificing quality. This is particularly crucial in industries where timing is everything.
Future Trends in Precision Injection Molding
As technology continues to evolve, the future of precision injection molding holds exciting possibilities. Here are some emerging trends that are likely to shape the industry:
1. Increased Automation
Automation technologies, including robotics and AI, are expected to revolutionize the precision injection molding sector. These advancements will lead to improved efficiency, lower labor costs, and enhanced precision in manufacturing processes.
2. Sustainability Trends
The push for sustainable manufacturing practices will drive innovation in precision injection molding. The development of bio-based materials and closed-loop recycling systems will become more prevalent, reducing the environmental impact of production.
3. Customization and 3D Printing Integration
With the rise of 3D printing, the ability to customize molds will become increasingly accessible. This integration will allow for faster prototyping and the production of more refined and tailored products, therefore enhancing competitive advantage in the market.
4. Advanced Materials
The introduction of new materials, such as lightweight alloys and composites, will expand the capabilities of precision injection molding. These advanced materials will enhance product performance while catering to specific industry requirements.
Conclusion: Harnessing the Power of Precision Injection Molding
In conclusion, precision injection molding is more than just a manufacturing process; it is a vital component of modern business strategies that seek efficiency, quality, and innovation. By choosing to engage with experts like Deep Mould, companies can harness this transformative technique to their advantage. The integration of precision injection molding into manufacturing not only promises enhanced product quality but also positions businesses to thrive in an increasingly competitive landscape.
For detailed consultation on how Deep Mould can assist your business in leveraging precision injection molding for greater success, do not hesitate to contact us today. Together, we can forge a path towards innovation and excellence in the manufacturing world.