Mastering Prototype Model Making for Architects
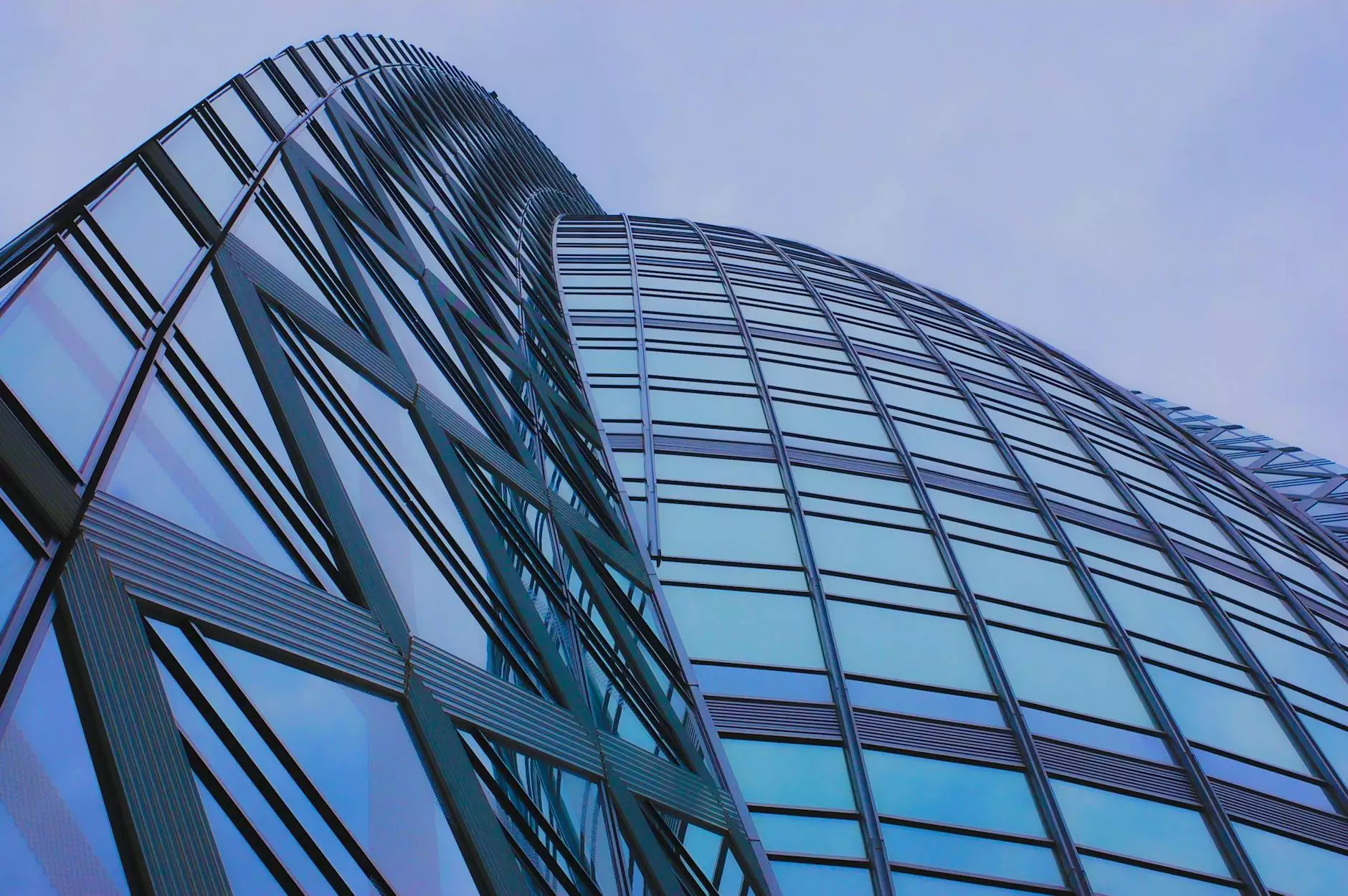
In the world of architecture, the importance of prototype model making cannot be overstated. It serves as a pivotal element in the design process, allowing architects to visualize their ideas in a tangible format. This article delves into the nuances of prototype model making, covering its techniques, benefits, materials, and how it can profoundly impact architectural design and client communication.
Understanding Prototype Model Making
Prototype model making is the process of creating physical representations of a design concept. Unlike mere sketches or digital renderings, models offer a three-dimensional insight into a project, making them invaluable tools in the field of architecture.
Why is Prototype Model Making Important?
The significance of prototype model making lies in its multifaceted benefits:
- Enhanced Visualization: Models provide a realistic view of architectural ideas, making it easier for clients and stakeholders to understand the vision.
- Improved Communication: A physical model can effectively bridge the gap between technical drawings and client expectations.
- Design Iteration: Creating models allows architects to explore various design options and rectify flaws before construction begins.
- Increased Engagement: Interactive models can engage clients more than static images or technical documents, fostering a better discussion environment.
Key Techniques in Prototype Model Making
To excel in prototype model making, architects can employ several techniques, each tailored to fulfill specific project requirements:
1. Scale Modeling
Scale models are an essential technique in prototype model making. They allow architects to represent a large structure in a manageable size that retains proportional details. The scale can range from 1:50 to 1:100, depending on the model’s objective.
2. Digital Prototyping
With advancements in technology, digital prototyping has emerged as a revolutionary technique. Software such as Rhino and SketchUp enables architects to create detailed models, which can then be fabricated using 3D printing techniques.
3. Physical Prototyping
Physical prototypes are crafted using various materials, allowing architects to experiment with form and function. This hands-on approach can lead to unexpected design solutions and innovations.
Crucial Materials in Prototype Model Making
Choosing the right materials is fundamental to the success of prototype model making. Here are some widely used materials:
1. Wood
Wood is a traditional and versatile material, offering durability and ease of manipulation. It’s particularly favored for architectural models due to its aesthetic appeal and structural integrity.
2. Foam Core
Lightweight yet sturdy, foam core boards are perfect for creating preliminary models. They are easy to cut and manipulate, making them ideal for fast prototyping and iterative designs.
3. Acrylic
Acrylic enhances models with transparency and a sleek finish. It is often used in high-end presentations to showcase modern designs and intricate details.
4. 3D Printed Plastics
3D printing has revolutionized prototype model making, allowing for intricate designs that are often impossible to achieve by hand. Various plastics can be used, offering flexibility in both form and function.
Steps to Create an Effective Prototype Model
Creating an effective prototype model involves a series of strategic steps:
Step 1: Conceptualization
The first step in prototype model making is to thoroughly understand the design problem. This involves brainstorming and sketching ideas, followed by discussions with team members or clients to solidify the vision.
Step 2: Material Selection
Choosing the appropriate materials for your model is crucial. Consider factors such as cost, durability, and how well the material represents the intended final product.
Step 3: Scale Determination
Define the scale of your model to ensure accurate representation. A properly chosen scale will also dictate the level of detail that can be achieved.
Step 4: Building the Model
With a clear plan, you can begin the construction of your model. Utilize different techniques to create various parts of the structure, ensuring to pay attention to detail as you progress.
Step 5: Refinement and Finishing Touches
Once the basic structure is complete, add details such as textures, colors, and landscaping to enhance realism. This not only improves the aesthetic appeal but also aids in better understanding the overall design.
Step 6: Presentation
A well-presented model can significantly impress clients and stakeholders. Consider the setting, lighting, and contextual elements when displaying your model to maximize impact.
The Role of Technology in Prototype Model Making
Technology plays a pivotal role in enhancing the efficiency and accuracy of prototype model making. Here are key advancements impacting the field:
1. 3D Printing
3D printing technology allows architects to produce complex forms and details quickly and accurately, which may otherwise be labor-intensive or impractical. The ability to iterate designs rapidly fosters more innovative solutions.
2. Virtual Reality (VR)
Integrating VR in the architectural process enables clients to 'walk through' designs before construction. This immersive experience can significantly enhance client understanding and satisfaction.
3. Building Information Modeling (BIM)
BIM integrates various building components, allowing architects to create comprehensive models that include data for materials, costs, and building performance. This technology enhances collaborative efforts and efficiency throughout the design process.
Challenges Faced in Prototype Model Making
Despite its numerous benefits, prototype model making presents certain challenges:
1. Time Constraints
Given the demand for quick turnaround times in architectural projects, creating detailed models can be time-consuming. Proper planning and prioritization are essential to balance speed with quality.
2. Budget Limitations
Model making can be costly, especially when incorporating high-end materials and technologies. Architects must navigate client expectations while staying within budgetary constraints.
3. Material Limitations
Not all materials allow for the same level of detail or represent complex designs effectively. Selecting the right material is imperative to convey the intended design accurately.
Best Practices for Successful Prototype Model Making
To ensure that your prototype model making efforts are successful, consider the following best practices:
1. Collaboration
Engage with your team and clients throughout the model making process. Their insights can provide valuable feedback that enriches the final product.
2. Documentation
Document each step of the model-making process. This not only helps in reflecting on the decisions made but also serves as a reference for future projects.
3. Continuous Learning
Stay updated on new materials, tools, and technologies that can enhance your model-making efforts. Attend workshops, webinars, and industry events to hone your skills continuously.
Conclusion: The Future of Prototype Model Making in Architecture
The significance of prototype model making in architecture will only continue to grow. As technology advances and architectural practices evolve, the integration of traditional craftsmanship with innovative technology will lead to unprecedented opportunities for architects. By mastering the art of model making, architects can enhance communication, improve design execution, and ultimately deliver extraordinary structures that resonate with their intended purpose.
Get Started with Your Prototype Model Making Journey
At architectural-model.com, we are dedicated to supporting architects in their quest for excellence in prototype model making. From expert tips to high-quality materials and workshops, we provide the resources you need. Start your journey today and elevate your architectural designs through the power of model making!